Whether you’re building a home foundry or you’re working in an industrial setting, you’re likely to encounter some casting defects when performing metalcasting.
This articles breaks down the common types of casting defects, and shows the various reasons they can occur.
Open shrinkage defects
Open shrinkage defects, like pipes and caved surfaces, form at the surface of the casting and burrow into the metal. Air compensation occurs as the shrinkage cavity forms.
Closed shrinkage
Sometimes called shrinkage porosity, closed shrinkage defects form within the casting. These defects can be seen with the naked eye (macro shrinkage) or only under a microscope (micro shrinkage).
Closed shrinkage defects sometimes appear at the top of hot spots, which are pools of liquid metal. To prevent shrinkage cavities, you can improve the casting structure by adding a shrinkage allowance to the pattern design before casting.
Open holes
There are several causes of blowholes, which are defects that appear on the surface of the cast. Poor venting and insufficient drying of mold and cores are two of the main causes.
Scars are shallow wounds that appear on a flat surface. Blisters are scars that are covered with a thin layer of metal skin.
How to Prevent Open Holes
To ensure good fluxing and melting practices, melt your metal in a non-oxidizing environment. This will prevent contact with the air.
To increase gas permeability of sand, use coarser sands. You can also let air and gas escape from the mold cavity. To dry out molds and cores before use, store them dry. To increase the rate of solidification, reduce metal temperature during casting.
Cuts and washes
Cuts and washes are defects that appear on the surface of a casting. They occur when molten metal erodes the molding sand, leaving a low projection along the surface.
Cuts and washes can happen when metal flows too fast, causing too much metal to flow through the gate. To prevent cuts and washes, you can design the gating system properly, improve mold and core strength, and add more binders to the facing and core sand.
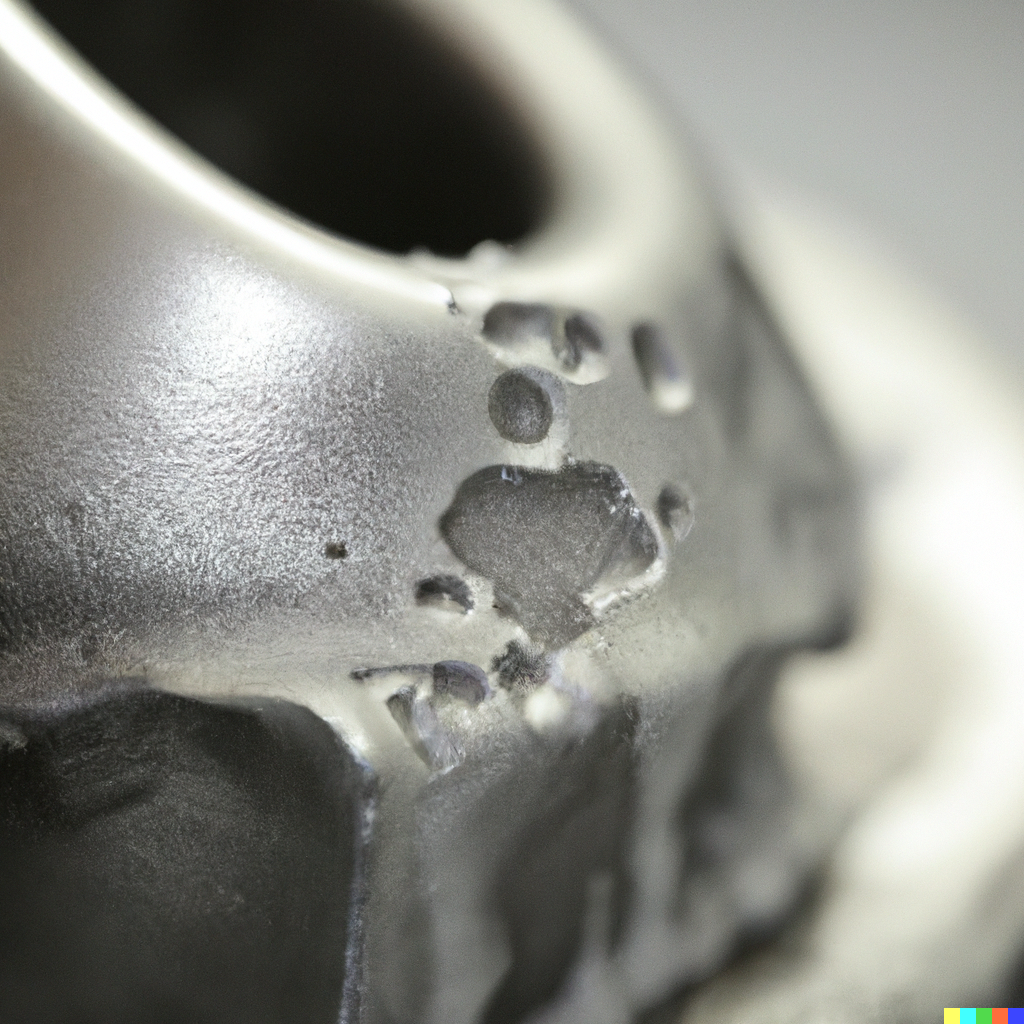
Sinks
Sinks are depressions on the surface of a casting that occur when there is a cavity present beneath the surface. These depressions are usually found along thick-walled areas of the casting.
Since sinks reflect light, they are easy to identify during a visual inspection. Sinks occur when the wall thickness of a casting is uneven, when the die cavity is partially overheated, when the die cavity is not properly ventilated, or when the injection pressure is low. To prevent sinks, the structural design of the casting should be optimized for an even wall thickness, the die cavity should be properly ventilated, and the injection pressure should be increased.
Slag Inclusions
A slag inclusion is a type of casting defect that occurs when non-metallic materials cause irregular crusts on the casting surface. This can reduce the mechanical characteristics of the final product. Slag inclusions usually have sharp edges and irregular shapes, and can be seen with the naked eye. Other types of inclusions include sand, nails, dirt, or oxides.
Slag inclusions are especially common when you’re melting dirty or unsorted metals, or thin metals like soda cans.
Runouts
Runouts happen when the molten metal leaks from the mold, resulting in missing or incomplete casted components. In most cases, the appearance is smooth, but you can also get irregular and rough runouts sometimes.
The same kinds of things can happen if you don’t have enough metal in the mold.
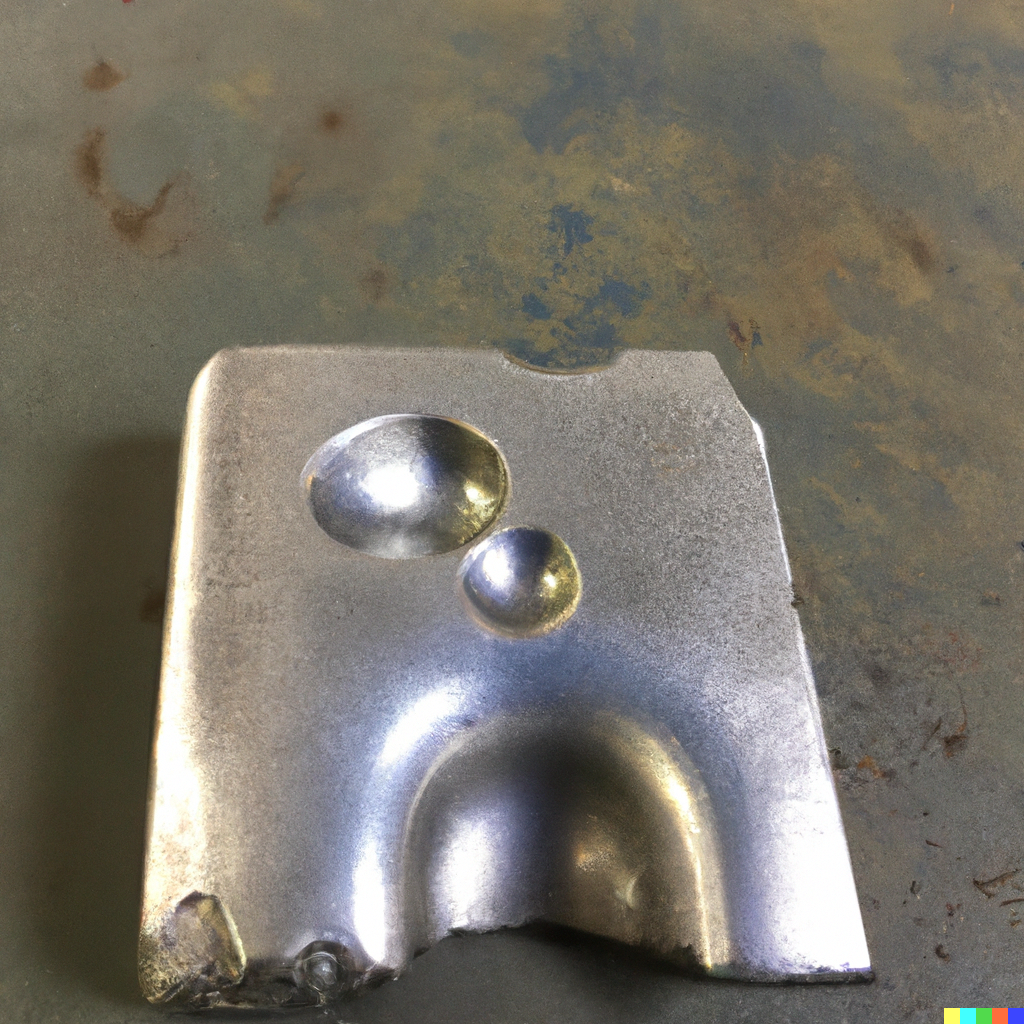
Rat Tails
Small lines or cracks on a casting surface are called rat tails, and they occur when the molten metal is too hot. The hot metal expands the molding sand, which causes the mold wall to move backward and give way. This leaves a small line on the casting surface.
If this happens several times during the casting process, you will see a crisscrossing of small lines on the surface of the component. Rat tails can be caused by poor expansion capabilities of the sand, improper mold design, or excessive metal pouring temperature. To prevent rat tails, add combustible additives to the molding sand, reduce the metal pouring temperature, or design the mold to be less hard.